Apparel Platform
In order to realize highly efficient and optimized logistics, we have prepared a collaborative delivery network, with logistics centers specialized in the apparel industry as its core component.
Customer's Challenges
CHALLENGE1Reduction of delivery costs to wholesale or retail shops
The products require delivery in small lots with quick delivery times, and the delivery costs tend to pile up. This customer of ours was searching for a way to resolve the issue of delivery costs.
CHALLENGE2Handling order volume fluctuations at fixed operation costs
Because logistics operation was being managed at own or external bases, the customer was incurring fixed cost for their personnel and warehouses. They were unable to adjust logistics costs to meet volume fluctuations flexibly.
CHALLENGE3Provision of VAS (value added service) to customers
Customer wanted to improve SCM In the distribution process; they wanted to have inspection for service quality improvement and also to outsource price tagging.
How LOGISTEED Solved Them
SOLUTION1Utilization of collaborative delivery networks
We arranged collaborative delivery for our customer, together with other apparel shipments from the same logistics center or other bases in the vicinity. Collaborative shipping can contribute to delivery cost reduction, as a third mode of your transport, complementing chartered trucks and scheduled route service.
SOLUTION2Network expansion of shared logistics centers
We have based our core facilities of apparel operations in the western region of Chiba Prefecture. By arranging the warehouse operations on the same floor or nearby, we can adjust the staffing in line with the seasonality, launch smooth operations, and share our management know-how.
SOLUTION3Provision of VAS in warehouses via distributive processing contracts
We also provide a broad range of optional services for distributive processing, such as inspection and price tagging. We provide a one-stop solution that adds value, from manufacturing completion till the end of the supply chain.
Some More Facts about the Value We Deliver
Strategic utilization of collaborative warehouse and delivery network can realize high quality sales logistics with great cost efficiency.
Collaborative warehouse and delivery network, targeting at shoes and sports apparel products
Management of client products in the shoes and sports apparel industry on the same floor. While maximizing cost performance in warehouse costs, we also optimize delivery costs by utilising joint delivery.
Abundant high-quality delivery experience with cost advantage
Our company's collaborative delivery network for shoes has achieved approximately 3,000 deliveries among Tokyo and five neighboring prefectures (Ibaraki, Tochigi, Saitama, Chiba, and Kanagawa). Our high-quality, cost-efficient, collaborative delivery network for shoes contributes to logistics cost reduction for our client, as a third mode of transport, complementing chartered trucks and scheduled route service.
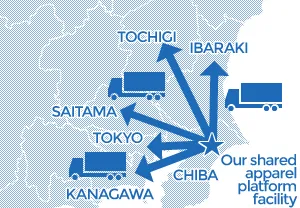
Providing you with even more value
With our collaborative delivery network for shoes, we are creating incremental value, such as supply cost reduction with reusable shipping cartons, which is difficult to realize with normal route service.
Snapshots of our work floor
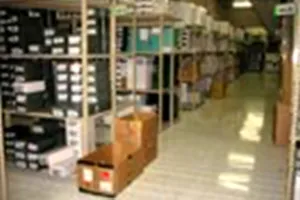
The floor layout of our logistics centers is designed for process optimization, with careful considerations for various requirements. We also realize very efficient inventory management.
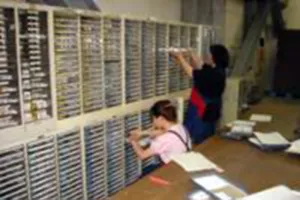
Our team of highly experienced staff conducts picking and price tagging with intense focus on safety and accuracy.
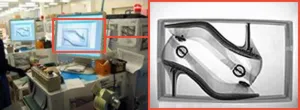
We are fully equipped with an X-ray inspection system. We also check the merchandise prior to shipping very carefully.