Re-engineering of chilled food delivery system
This is a case example where by centralizing the point of contact, constructing a thorough temperature control system, and promoting real-time visualization, we achieved optimal inventory management and delivery quality improvement in chilled food sales logistics.
Customer's Challenges
CHALLENGE1Holistic SCM improvement was no easy
Our customer was managing warehouse work by themselves and using one of the group companies for delivery. Neither of them was quite willing to let go of their existing interests, making it hard for them to cooperate with each other. Improving the SCM overall was a challenge in this situation.
CHALLENGE2Maintenance of quality control
Their existing logistic center was cramped and aging, and they were concerned about whether they could maintain the quality control in the future.
CHALLENGE3On-site inefficiency
There was a great deal of manual work in the warehouse, leaving a room for improvement in terms of efficiency, but reforms were only slowly progressing with such initiatives delegated to the floor.
How LOGISTEED Solved Them
SOLUTION1Improvement by centralizing the point of contact
Placing the management of warehousing and delivery under our control, we centralized the point of contact for our client. After we took over the coordination between the warehouse and delivery function, we realized overall improvement in logistics.
SOLUTION2Thorough temperature control
We established a new operational base, with considerations on how we should operate on each floor, in order to manage the temperature control thoroughly. Furthermore, we reinforced on-site staff awareness through training and education, regarding each work procedure inside the new facility. These multifaceted efforts have resulted in our consistently high quality service.
SOLUTION3Real-time inventory information
Implementation of a system that enables uniform management of logistics information. Visualization using a management system enabled us to capture the incoming and outgoing cargo progress real-time. By identifying where to eliminate waste inventory, we support our customer to enhance their profitability.
Some More Facts about the Value We Deliver
Despite handling chilled food is regarded challenging in general, we provide robust quality with our abundant experience and strong expertise.
Our proposal in detail
After careful considerations of customer's requests, we proposed our logistics solutions, including the warehouse mapping, the systemization of warehouse operations, and a staffing plan.
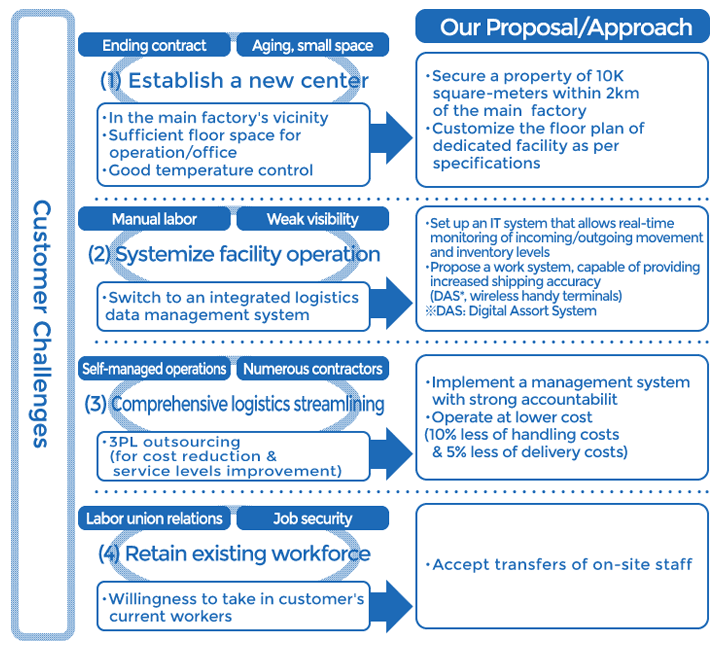
Overall SCM flow after improvement
We have implemented comprehensive SCM improvement from warehouse management to delivery. By placing all the logistics function under our control, we are able to enhance SCM holistically.
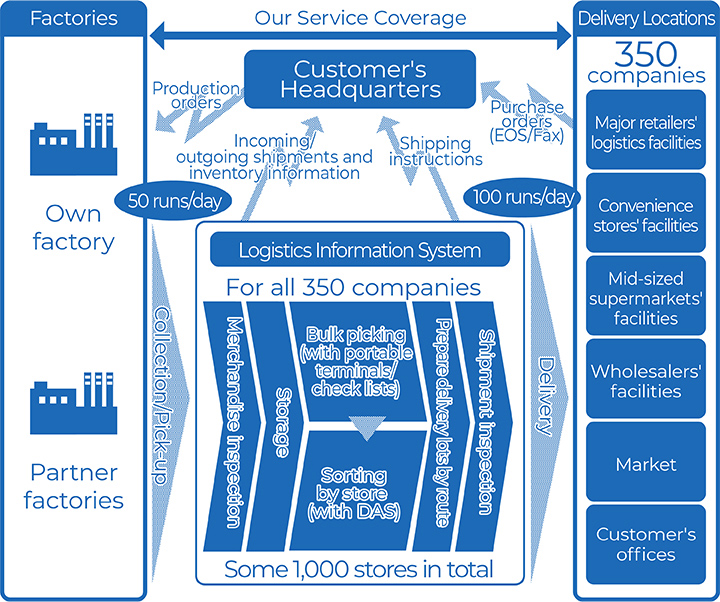