Optimization of service parts center
This is a case example where we reviewed the logistics operations in Japan for a customer, who provides service parts around the world, and helped them increase the efficiency, optimize inventory, and improve client services. By rationalizing the service parts supply chain management with Japan's facility in its center, we resolved many of their problems.
Customer's Challenges
CHALLENGE1Reduction of delivery lead times
In order strengthen overseas sales competiveness and the service level, they were hoping to reduce delivery lead times
CHALLENGE2Occurrence of duplicate work due to decentralization of inventory bases
Because the inventory bases were decentralized in each area, there was duplication in their work, resulting in wasteful operations and inventory surplus.
CHALLENGE3Shipping capacity limits
Their existing automated warehouse was 10 years old and aging. Old machines specifications were limiting the shipping capacity, and the construction of a better shipping system was essential.
How LOGISTEED Solved Them
SOLUTION1Consolidation of decentralized inventory bases
Centralization of inventory management functions from different places around the country into one location. We were able to compress the inventory space and streamline the staffing, leading to better cost efficiency.
SOLUTION2Changing client systems to EDI
Through EDI coordination with the customer's host system, shipment information for customs documents is now automatically received. Shipping within the day of order became possible, even for exports. Through accurate and speedy delivery response, we provide support for maintaining and improving customer satisfaction. Of course we have also realized EDI with the customs.
SOLUTION3Highly efficient warehouse management
Productivity improvement of conveyance, storage, and picking by adopting conveyer transport and relay pick methods. We are also eliminating idle time and waste procedures, by calculating the size and number of packing boxes concurrently with the packing work, prior to preparation of package labels and packing lists.
Some More Facts about the Value We Deliver
With our extensive network in and out of Japan, we can provide solutions for you to cope with your global SCM challenges, building on our operational expertise as well as cutting-edge information technology (IT) and logistics technology (LT).
Footprint, methods, and systems with an eye on global expansion
Striving for optimization of base management and logistics reform from a global viewpoint, we have conducted SCM operation reengineering first on operations in Japan. We provided our customer with rationalization proposals with a placement of a strategically integrated logistics center in Japan at the core of the renewed supply chain.
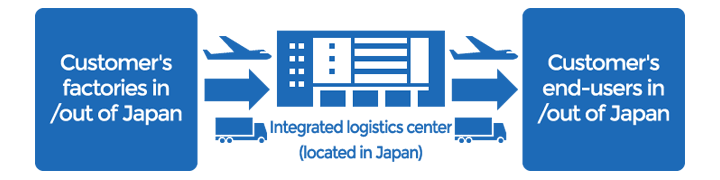
Our new model of global logistics system is achieving overall optimization, with better inventory management efficiency and cost performance.